![]() |
|
Biography
Lado Filipovic studied electrical engineering at Carleton University, in Ottawa, Canada, where he received the degree of Bachelor in electrical engineering (B.Eng.) in 2006 and Master in applied science (M.A.Sc) in 2009. He joined the Institute for Microelectronics in January 2010, where he completed his doctoral degree in December 2012, which focused on topography simulations of novel semiconductor processes. Since then his scientific interest have broadened to studying and modeling the effects of fabrication-induced variability on semiconductor geometries and their application in the fabrication of quantum metrology devices. His added research interests involve the design and simulation of environmental sensors and, more specifically, using metal oxide semiconductors for the detection of toxic gases and pollutants.
Reliability of Metallic Microheaters for SMO Gas Sensors
The essence of how we perceive the environment is in large part shaped by the presence of various gases in our vicinity. As a natural sensor, the human nose can detect hundreds of different odours, but it fails absolutely in determining which gas is harmful or in detecting specific gas concentrations. Sensors are playing an ever-increasing role in our everyday lives, culminating in the recent advances in the development of wireless sensor networks and the Internet of Things. Attempts at system-on-package integration lead to the use of long wires, which result in high resistive-capacitive delay and increased circuit resistance, limiting the device lifetime. An improved integration technique, deemed System-on-Chip and 3D integration, is used to ensure the fabrication of all components on a single substrate (see Fig. 1).
The semiconducting metal oxide (SMO) gas sensor has proven itself the gas sensor of the future, and its technology has already begun commercialization. However, further miniaturization and power reduction are essential for this sensor to enter the mobile market. For this, the SMO sensor's integration with analog and digital electronics using CMOS fabrication techniques has been attempted in order to reduce power consumption and fabrication costs. The SMO gas sensor works through the chemisorption of gas molecules on its surface at high temperatures, in the range of 250℃ to 500℃. This high temperature is enabled by the integration of a micro-sized hotplate, which requires isolation from other elements using a suspended membrane. This hotplate is the primary consumer of power in the sensor. Reducing its power therefore requires a significant reduction in the total sensor power dissipation. To improve the uniformity of the temperature distribution and to minimize thermal losses, several unique geometries have been introduced, shown in Fig. 2.
An added concern for the metallic microheater structures is their long-term reliability under a strong electric field and high thermal gradients. Under these operating conditions, electromigration can significantly limit the device lifetime, which needs to be properly modelled. Continuum models for electromigration, which treat the metal layer as a single bulk entity, are not sufficient since they do not take the microstructure into consideration. The resistivity of metallic films is increased due to electron scattering at the grain boundary, meaning that the resistivity can no longer be treated as a bulk material property, and a microstructure-dependent implementation is essential, as shown in Fig. 3. In addition to the change in conductivity, the electromigration reliability is also heavily influenced by grain boundaries and material interfaces. They play a significant role in atom diffusion and vacancy generation and annihilation, allowing for an effective speed-up of the electromigration phenomena. With a novel method of treating the conductivity and atom diffusivity as spatial parameters, we can use coarse meshes to obtain accurate simulations while taking the granular microstructure into account.
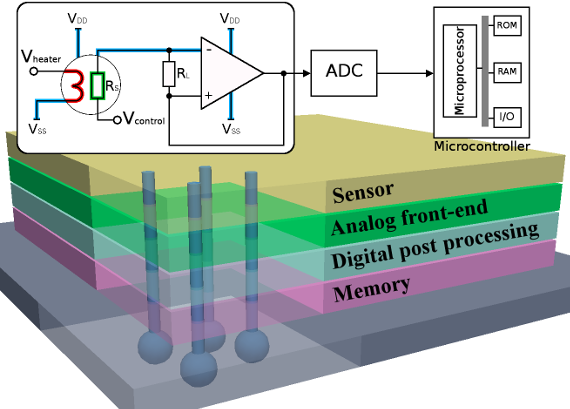
Fig. 1: 3D integration of a sensor using through silicon vias.
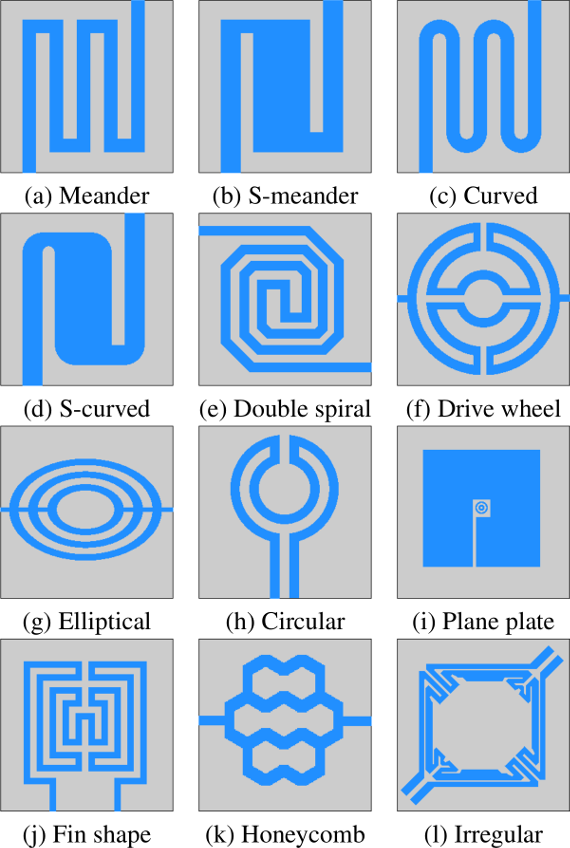
Fig. 2: Different microheater geometries characterized and modeled by various research groups.
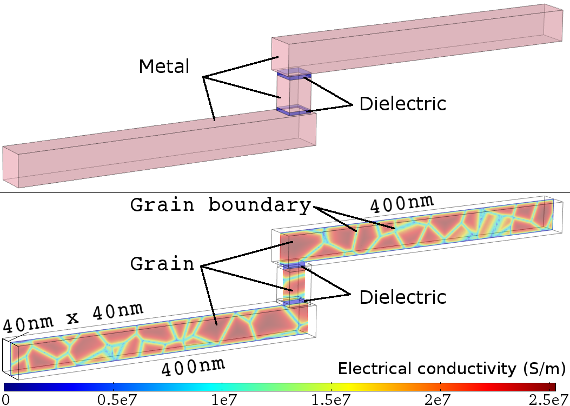
Fig. 3: Grain-dependent conductivity in a metal interconnect.