![]() |
|
Biography
Ayoub Lahlalia was born in Agadir, Morocco, in 1992. He obtained his M.Sc. degree in microsensors and detection systems from Aix-Marseille university, Marseille. France, in 2016. He joined the Institute for Microelectronics in March 2017, where he is working on his doctoral degree. His scientific interest focuses on Metal Oxide Semi-conductor Gas Sensors dedicated to wearable devices.
Improved Capability of Integrated Semiconducting Metal Oxide Gas Sensor Devices
Nowadays, the demand for gas sensors suitable for use with wearable devices has received much consideration. This interest is principally driven by the increased market size for gas sensors for consumer applications and rising concerns about outdoor air pollution. In 2014, the World Health Organization reported that around seven million people die each year; one in eight of total global deaths was as a result of exposure to air pollution. In order to get out from underneath the trap of using components that pollute our surroundings, however, one effective solution is to raise awareness of how vulnerable we are to the impacts of climate change. This can be done by making gas sensors available to everyone through integration with handheld devices, such as smartphones and wrist watches, which would allow is to monitor air quality easily at anytime and from anywhere.
In fact, the development of novel gas sensors based on metal oxide dedicated to wearable devices is still in progress, and the necessity for reliable sensors, along with high selectivity and ultra-low power consumption, is one of the greatest challenges of semiconducting metal oxide (SMO) gas sensor development. However, several limitations and drawbacks must still be overcome before the monolithic integration of a gas sensor into portable devices. Fig. 1 shows two novel structures of the SMO gas sensor, namely a microheater array and dual-hotplate design, which meet different sensor designers' needs, such as a uniform thermal distribution, ultra-low power consumption, high selectivity, electrode definition and low membrane deformation.
The microheater array design consists of a combination of small resistances placed in an array instead of a conventional microheater (Fig. 2a) and is used for heating the sensing layer at different locations and at different temperatures. This allows for an improvement in the desired temperature distribution over the sensitive material while reducing the power consumption. In addition, small resistances allow for an ultra-fast thermal response time, which enables the microheater to operate in an ultra-short pulsing mode, thus reducing the average power consumption to a few hundred microwatts. The locations of the small heaters have been optimized in such a way that the active area operates at a high temperature uniformity, with variation within 10 °C. This feature has been used to improve the selectivity of the thin film metal oxide by gathering multiple sensing layers onto the same membrane structure. Since the sensitivity of thin metal oxide films to gases depends on the operating temperature, each sensing layer is heated to a specific temperature, which remains uniform over the desired sections.
The dual-hotplate sensor is a novel design that uses a single circular microheater, along with two passive micro-hotplates (Fig. 2b). These are used for the purpose of improving the temperature distribution over the sensing layer, while keeping power consumption to a minimum, which is critical for baseline stability. A small variation in temperature over the sensing layer leads to baseline drift, thereby creating a change in the resistivity of the sensitive material. In addition, working at a heterogeneous temperature activates more interactions between gases and the sensitive layer, which influences the selectivity and stability of the sensor. The operating principle of this novel structure relies on the high thermal conductivity of platinum compared to silicon dioxide and silicon nitride, which means that the heat flux through the Pt dual-hotplate is greater than the heat flux through the membrane. By optimizing the position of theses two metal plates, the uniformity of the temperature can be improved.
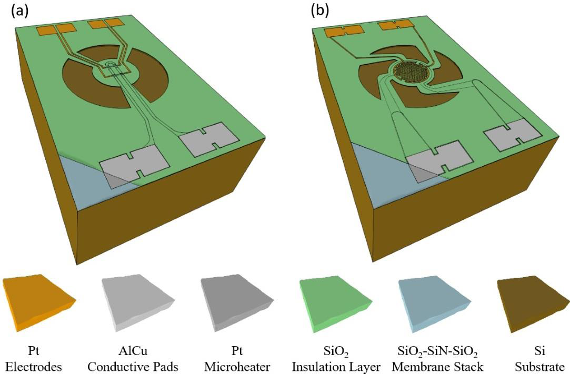
Fig. 1: Novel structures of the SMO gas sensor: (a) Microheater array design; and (b) dual-hotplate design.
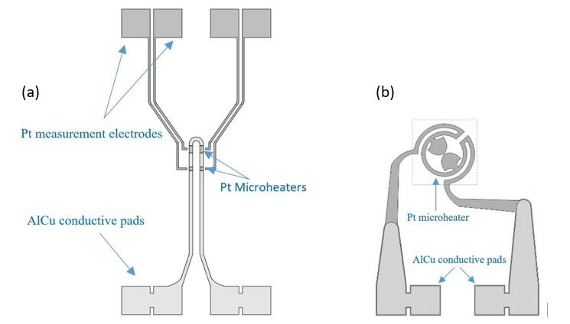
Fig. 2: Structure of the microheater, along with conductive pads: (a) Microheater array design; and (b) dual-hotplate design.