![]() |
|
Biography
Lado Filipovic studied electrical engineering at Carleton University, in Ottawa, Canada, where he received the degree of Bachelor in electrical engineering (B.Eng.) in 2006 and Master in applied science (M.A.Sc) in 2009. He joined the Institute for Microelectronics in January 2010, where he completed his doctoral degree in December 2012, which focused on topography simulations of novel semiconductor processes. Since then his scientific interest have broadened to studying and modeling the effects of fabrication-induced variability on semiconductor geometries and their application in the fabrication of quantum metrology devices. His added research interests involve the design and simulation of environmental sensors and, more specifically, using metal oxide semiconductors for the detection of toxic gases and pollutants.
Gas Sensor Integration in Advanced CMOS Technology
The ability to incorporate gas-sensing devices into wearable technology, such as smart phones, tablets and wrist watches, will revolutionize the environmental health and safety industry by providing individuals with a convenient way to detect harmful chemicals in the environment. Although thin metal oxide (MOX) films have demonstrated their gas-sensing capabilities, several challenges must still be overcome in order to enable full CMOS integration with reduced costs of production and low power consumption.
Power consumption is mainly driven by the need for a microheater to heat the sensing layer up to 500℃. The design of a microheater must ensure good thermal conformality across the sensing membrane and low power dissipation. Many materials, including Au, Au/Ti, Al, Ni (+alloys), W, Pt and polysilicon, have been tested for microheater fabrication, each with their own advantages and disadvantages.
Pt microheaters are promising for gas sensing because they have a suitable thermal resistance coefficient, can handle large current densities, can operate at 550℃ to 600℃ without structural damage, and are reliable and reproducible. The common "Meander" microheater design, shown in the bottom left corner of Fig. 1, has proven to be inefficient due to a poor resulting temperature distribution. A double-spiral microheater is the preferred design for temperature uniformity across the sensing membrane, as shown in Fig. 1. The sensing membrane is composed of the microheater sandwiched between two thin silicon dioxide layers. The half-pitch of the Pt wires used for the heater is 0.5μm.
In addition to the microheater fabrication, the deposition of the sensing layer itself must be integrable with the CMOS sequence to ensure the financial feasibility of the full device. Recently, spray pyrolysis has been examined as a potential option, as it can be used very cheaply to deposit MOX layers down to thicknesses of tens of nanometers. Many layers have been tested, with SnO2, ZnO and WO3 showing the most promise.
In order to model the sensing mechanism, a multi-stage model is necessary. First, oxygen chemisorption is modeled, including the surface reaction of the chemisorbed oxygen with a reacting gas. Second, after calculating the steady state of the reactions in the previous step, the surface charge distribution is derived, which is used to find the depth of the depletion region and the electrostatic potential distribution inside the MOX layer. A simple schematic of the resistances in play for a SnO2 compact layer is shown in Fig. 2.
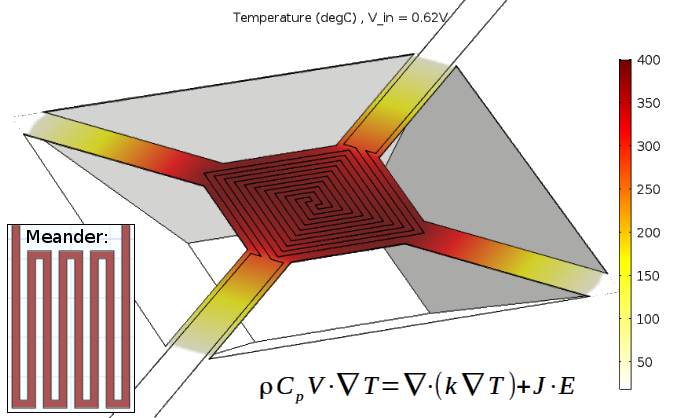
Fig. 1: Temperature distribution in a double-spiral Pt microheater, suspended over a cavity.
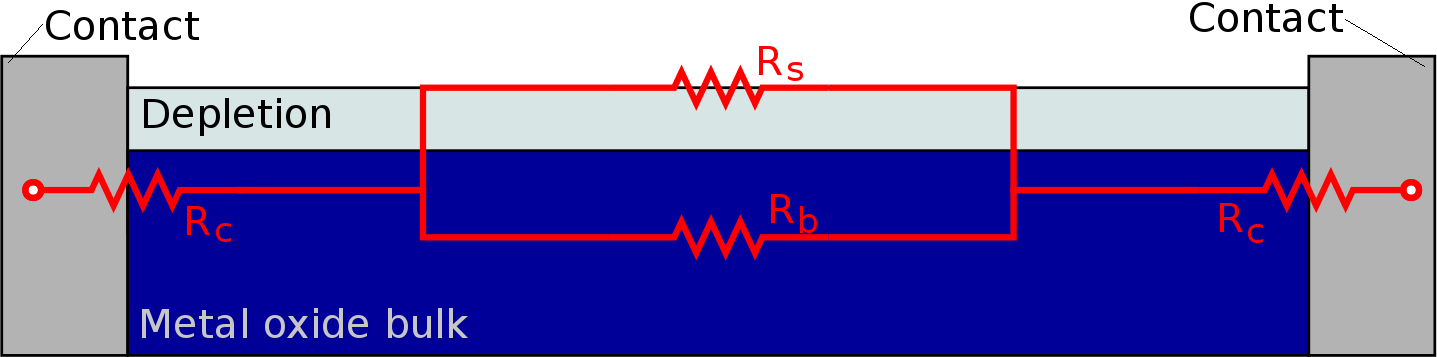
Fig. 2: Resistances active during the operation of a compact metal oxide gas sensor.