![]() |
|
Biography
Lukas Gnam was born 1991 in Wr. Neustadt, Austria. He received his Bachelor's Degree in Technical Physics and his Master's Degree in Physical Energy and Measurement Engineering from the Technische Universität Wien in 2014 and 2016, respectively. After finishing his studies he joined the Institute of Microelectronics in April 2016, where he is currently working on his doctoral degree. His research focus is on high performance parallel mesh generation algorithms.
Towards a Metric for an Automatic Hull Mesh Coarsening Strategy
In numerical simulations in various areas of science and engineering (e.g. biomechanical engineering or ray tracing), the discretization of objects in physical space is an integral step. This is particularly relevant in three-dimensional cases, where volume mesh generation is required. Mesh generation is critical to ensuring the robustness, stability and accuracy of subsequent simulation steps.
One common approach to generating a volume mesh utilizes the advancing front method. This approach uses a two-dimensional hull mesh (i.e. a closed surface) as its starting point, which potentially consists of an unnecessarily large amount of mesh elements. Obviously, the properties of the hull mesh (e.g. the number of triangles and their quality) heavily influences the quality and execution time of the volume mesh generation process, as well as subsequent simulations.
We investigated a novel combined comparison metric to compare the quality of the coarsened mesh to its original input.
The Computational Geometry Algorithms Library's triangulated surface mesh simplification algorithm was utilized to coarsen two widely used and representative geometries (see Fig. 1). To evaluate this algorithm, we selected four widely used metrics to capture various aspects of the coarsening process. We picked the triangle shape quality, the geometric distance to the original mesh, the differences in curvature and the surface area deviation.
Using these metrics, we devised a combined quality metric, which maps all aspects to a single scalar-valued metric. This combined metric depends on four weighting factors, which have to be determined empirically with respect to the actual application in mind. Our studies show that these weighting factors depend heavily on the input geometry. This is due to the fact that the way that the four metrics change between the original and the coarse mesh depends on the number of removed triangles, which is mesh specific.
Our investigation into the possibility of combining a coarsening algorithm together with a combined quality metric is the first step towards devising an automatic hull mesh coarsening work flow. In the future, we will focus on analyzing domain-specific weighting factors and on devising an automatic method with which to compute them.
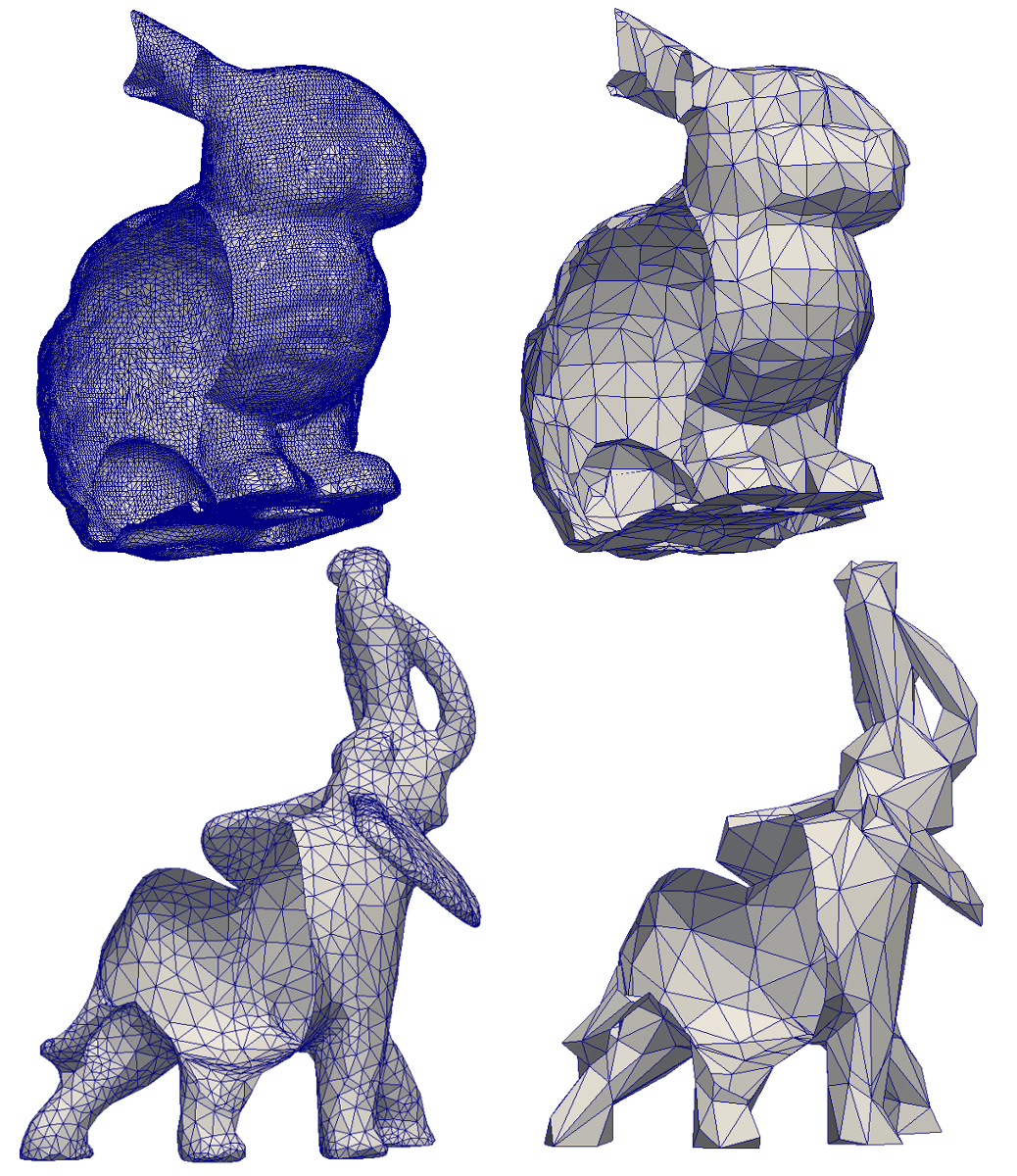
Fig. 1: Cross-sections of the original and exemplary coarsened meshes of the two test geometries. The bunny in the top row was coarsened from 69,451 to 1,513 triangles, the elephant from 5,558 to 554.